Hier mal ein kleiner bericht um alle Fragen rund ums Bohren von Löchern aller größe z.B. für Lüfterlöchern, Windows, Halterungen für AGBs, uvm. usw.
Da es zu diesem bereich der Werkstoff bearbeitung immer wieder zu Fragen kommt will ich hier mal einige der geläufigsten Bohrarten aufzählen und jede etwas bescheiben!
So hier mal die wichtigsten Bohrmetoden:
- Mit einem Handelsüblichen Bohrer (z.B. HSS, Hartmetall)
- mit einem Stufenbohrer
- mit einer Lochstanze
- mit einer CNC gesteuerten Fräsmaschine
- mithilfe einer Drehmaschine
- einer Oberfräse
- mit einem Kreisschneider
- mit einem Lochschneider
Boherer:
Das Thema Boheren werde ich etwas ausführlicher beschreiben da man ja schon einiges darüber weis!
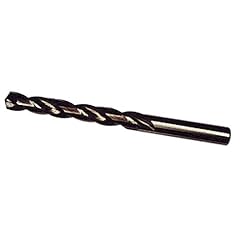
Es gibt viele unterschiedliche arten von Boherern mit unterschielicher Form und Materialart:
- HSS (Hochleistungs schnell schnitt Stahl) Boher
- (Voll-) Hartmetall Bohrer
- Boherer mit Wendeschneidplatten (Hartmetall, Keramik, Diamant)
- Titanbeschichtete Boherer
- Holz, Stein usw. Boherer
Handelsübliche Spiralboherer gibt es bis zu einer größe von ca. 75mm (bei so einem Modell muss man mit einem Preis von ca. 1000€ reichnen aber zum Glück gibt es ja noch andere Bohrverfahren) Ab einen Bohrdurchmesser von 10mm gibt es bohrer mit Keglichen oder Konischen Schäften. Hier muss einfach nur das Bohrfutter aus der Maschine genommen und der Raum zwischen Bohrer und Spindel durch Mossekegel ausgegeicht werden!
Bohern kann man auf verschiedenen Bohrmaschinen z.B.
-Tischbohrmaschine: Auf einem Tisch montiert. Bohrdurchmesser max. 10mm. Für kleine Werkstücke.
-Säulenbohrmaschine: Tisch höhenverstellbar und drehbar (360°). Für kleine und mittlere Werkstücke
-Stenderbohrmaschine: Tisch nur höhenverstellbar und abgestützt. Mit Vorschubeinrichtung. Für große Werkstücke
-Radialbohrmaschine: Radial und axial verstellbar, dadurch Herstellung meherer Bohrungen in einer Aufspannung möglich!
- Lehrenbohrmaschine: Fertigen von genauen Bohrungen und Abständen bis zu einer Genauigkeit von 0,02mm
- Handbohrmaschhine: Ohne Befestigung also tragbar. Bohrdurchmesser max. 10mm. Für alle Werkstückgrößen geeignet. Maßhaltiges Bohren kaum möglich!
Bohren kann durch Reiben, Winkelsenken, Zylindersenken, Hohnen uvm. ergänzt werden!
Habt ihr Probleme beim Bohren!? Hier sind mögliche Fehlerquellen:
- Zu großer Bohrdurck
- Die Scheidenwinkel sind ungleich (Bohrer verläuft)
- Falsche einstellwerte (z,B. Drehzahl)
--> Hier die Tabell um die Drehzahl fast aller Werkstoffe heraus zu finden: http://www.xn--bnting-3ya.com/html/drehzahltabelle.htm
- Bohrspitze liegt außerhalb der Bohrer-achse (Bohrloch zu groß)
- Nicht oder ungenügend angekörnt (Bohrer verläuft)
Stufenbohrer:

Ein Stufenbohrer besteht meistens aus HSS und einen Duchmesser von max. 60mm erreichen! Bei einem Stufenboher ist stehts zu beachten, dass man ihn nur mit halber Drehzahl und gut gekühlt verwendet. Da er sonst schnell verschleisst und stumpf wird!
Ein Stufenbohrer kann nur verwendet werden wenn schon ein loch vorhanden ist! Außerdem kann man mit ihm nur Blech bis zu einer dicke von 5mm bearbeitet werden.
Lochstanze:

Mit einer Lochstanze kann man Maßgenaue Löcher in dünne Bleche schneiden hierbei muss sie durch ein vorhandenes kleines loch geführt und mit zwei Schraubenschlüsseln zusammengeschraubt werden. Hierbei wird die Schneide langsahm durch das Material gezogen bis es abgertennt wurde. Bei dieser Metode benötigt man je nach Material viel Kraft erhält aber ein sauberes Lochergebnis!
Eine Lochstanz wird meistens für Badamaturen o.ä verwendet! Ist aber gut geeignet um Löcher für Kabel, Wakü Schläche uvm. zu bohren, die aus dem Case verlegt werden.
CNC gesteuerte Fräsmaschine:

Zu Thema CNC technik werde ich in einem kommenden Berich etwas Detailierte eingehen! Hier aber das wichtigste zum Thema Bohren in einem CNC-Fräszentrum.
Eine CNC-Fräsmachine kann löcher in fast allen größen und in fast alle Werkstoffe fräsen. Da die Maschine aber digital ist bestehen alle Kreise und Rundungen aus vielen ecken die aber eigenlich nicht mal richtig erfühlt werden können aber sie sind da! Gebohr bzw. gefräst wird mit Handelsüblichen Schaftfrästern die aus HSS, Hartmetall oder mit Wendeschneidplatten bestuckt besthen können.
Der nachteil man kann keine unstabielen teile Fräsen also muss alles zerlegt sein um die nötige Stabilität und Sicherheit zu garantieren!
Drehmaschine:

Das drehen von löchern in Drehmaschinen ist nur in kleine Werkstücke möglich da nur ein eingeschrenkter Drehradius oder Spannbereich im Backenfutter gegeben ist! Es können aber sonst fast alles in der Drehmaschine gebohrt werden durch Auswuchten und spezielle Spannvorrichtungen ist das Bohren auch auserhalb der mitte möglich!
Oberfräse:

Das fräsen von löchern, die auch wirklich Rund sein sollen ist nur mithilfen einer Schablone möglich! Hierbei wird die Oberfräse auf einem Restmaterialstück oder einer Verstellbaren Schablone befestigt und im gewünschten Radius und am gewünschten Platz der Mittelpunkt des Kreises Platziert. Gefräst wird mit einem Walzenstirnfräser o.ä. Mit einer Oberfräse kann man nur weiche Materialien bearbeiten z.B Holz, und weiche Kunsttsoffe.
Kreisschneider:

Mit einem Kreisschneider werden Bleche und ähnliche Werkstoffe bearbeitet z.B Plexiglas usw. Ein Kreisschneider besteht aus einem Bohrer, einem Abstandshalter und einem Schneidewerkzeug. Er kann nur in Feststehenden Bohrmaschinen verwendetwerden da schon bei der kleinsten Anstellwinkelabweichung es zu unfällen kommen kann, da ja nur eine schneide vorhanden ist!
Lochschneider:
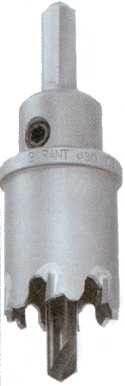
Ein Lochschneider oder auch Lochsäge, wird normalerweise zum heraussägen von Steckdosen verwendet! Es gibt sie aber auch in anderen ausführungen mitdenen man Metall o.ä. bearbeiten kann. Zur führung und zur justierung der Bohrungsmitte befindet sich ein Bohrer im Zentrum des Lochschneiders.
Wenn noch jemand Fragen dazu hat oder Verbesserungsforschläge kann er sie hier mitteilen!
mfg chopper 